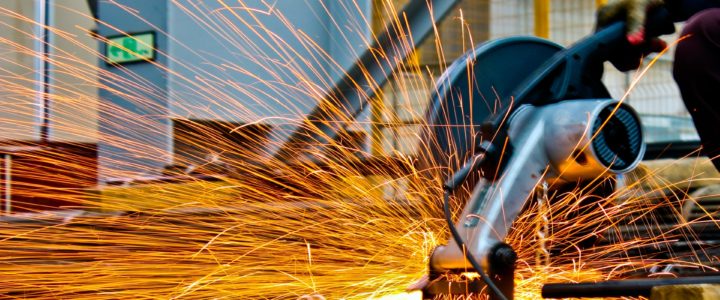
Steel provides the necessary framework for roads, bridges, railways, housing, and every type of transportation modality. It’s also used in abundance in household appliances like fridges, cooking utensils like saucepans, furniture, and surgical instruments. It seems even more unavoidable than plastics. And that’s not a bad thing. Steel is infinitely recyclable with no downgrading in quality, so once manufactured it’s life is potentially limitless. Even scrap from the smelting is fed back into the system for use. Due to being magnetic, it’s extremely easy to separate from other recycling/trash. And recycling steel uses 64% less energy, 73% less GHGs, and 90% less iron ore than when processing virgin steel. There is more demand than supply for recycled steel, which maintains the value of this commodity—something which can’t be said for most other recycled materials. But the rates for steel recycling are pleasingly high. In 2018, ferrous scrap in cars was recycled at 106%; structural steel was 98%; appliances had a 90% rate; reinforcement steel was recycled 70% of the time, and steel cans had a recycling rate of 66.8%.
Let’s take a quick look at what steel actually is. You might immediately think of it as a metal. But in fact it’s an alloy—a composite material from different types of metals—of iron (the major component), carbon, manganese, nickel, chromium, silicon, and cobalt. The exact ‘recipe’ used will determine the characteristics of the resultant steel and hence the function of it. Specific things which change according to the combination of metals used (but all of which are much higher than in the individual metals) are melting point, density, hardness, strength, flexibility, and tensile strength. The grading of the various steel output is usually done by the carbon content. Low-carbon steel is that which contains less than 0.25% of carbon; medium-carbon steel contains 0.25% to 0.55% carbon; and high-carbon steel has anything from 0.55% upwards. But if there is more than 2% carbon, the result is brittle and the use cases are much more limited.
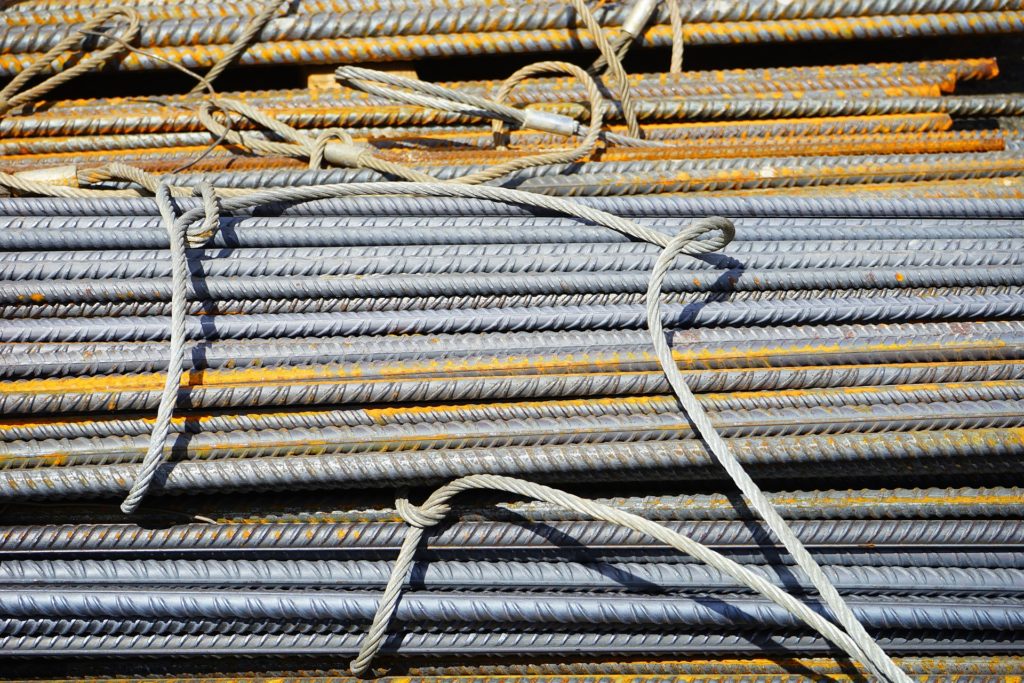
It’s clear then, that steel is not going anywhere. It really is a necessity in our lives, functionally and economically. The industry employs millions of people worldwide, has an annual turnover of $2.5 trillion, and produces over 1.3 billion tons of the stuff every year. Thanks to developments in materials science, we need less to create the same products than ever before—if the Eiffel Tower were built today, it would require 75% less steel. While we’re looking for alternatives to cement and plastic, due not only to the raw ingredients and large carbon footprint of production, but largely to the end-of-life difficulties with these materials, luckily we need not find a replacement for steel. But what we do need to address is the manufacturing process. Because as it stands, outside of power generation, the iron and steel sector is the largest industrial producer of GHGs. A whopping 7-9% of global direct fossil fuel emissions are from this industry—more than the total emissions from India. This is a relevant statistic because India is currently the world’s second largest steel manufacturer, and plans to be the leader with 20% of the world’s production by 2050.
There are two main methods of steel production: blast furnace (BF) or electric arc furnace (EAF). Usually, when virgin steel is being produced the BF method is used and it can utilize a maximum of 30% recycled steel; where EAF can utilize 100% recycled material. The move from BF to EAF has already resulted in a 60% decrease in energy requirement. There is a firm trend toward more EAF so it’s hoped that this already improved energy efficiency could improve further, but it should be noted that these actions alone won’t be enough to decarbonize the industry adequately. The International Energy Agency calculate that the industry need to drop emissions by at least 50% by 2050, if we are to meet global energy and climate goals. The blast furnace technique requires large quantities of coking coal, a high quality coal, and this is used for heating energy (temperatures above 1,000°C, which separates the oxygen molecules from iron oxide) as well as playing a part in the chemical reaction of production. When we say ‘large quantities’, we mean it—in Germany the steel sector uses 1/3 of their total coal demand. Typically, it takes 1.6 tons of iron ore and about 450kg of coke to produce a ton of the raw iron which comes out of a blast furnace.
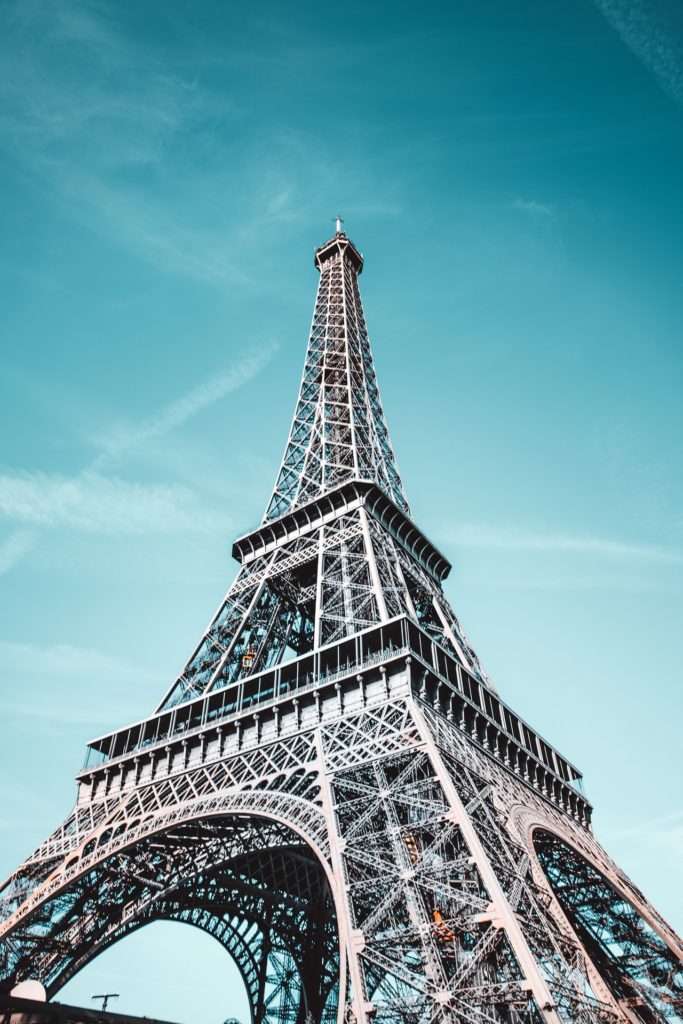
A by-product of this chemical reaction is CO2, because the cheapest way to obtain the extreme heat required is with coking coal. However, this is where Japanese steel manufacturer Kobe Steel are focusing to make a positive impact: they’ve been adding hot briquetted iron (iron ore with the oxygen removed) to the furnaces, so they need less coking coal. They suggest that their technique will reduce GHG emissions by 20%.
Another option for reducing steel production’s environmental footprint, while still using BF technology, is utilizing green hydrogen as the reductant instead of coking coal. This means the only by-product is water, no CO2 at all. An exciting collaboration on this front is in Sweden, between an investor group, a sustainable innovations accelerator, and a trucking company, and is called H2 Green Steel (H2GS). They expect to go into production by 2024 and by 2030 will be making 5 million tons of high quality zero emissions steel, every year. They are focused on providing steel to the transport industry. Looking at car manufacture specifically, Mercedes-Benz claim that one sedan is about 50% steel – which makes up 30% of the vehicle’s production GHGs. So this move has incredibly powerful potential. The key to make it a reality will be the availability of cost competitive green hydrogen. Until that happens, there will likely be an increase in the cost of steel. Customers need to acknowledge the reason for this and swallow the temporary bitter pill. Will that happen? We have to hope so.
Another innovation is from Bill Gates backed start-up, Boston Metal. They aim to separate the oxygen from the iron ore using electricity, creating a by-product of oxygen, through a process called Molten Oxide Electrolysis. They’ve had success in the labs at MIT and now need to scale and commercialize. The benefit of this over the use of green hydrogen is that they can get to the end result—high quality steel—faster, with fewer steps. But a major similarity with green hydrogen is that this tech won’t come cheap. So the need for taxpayer support is inevitable.
Investment and innovation are playing a integral role in decarbonizing this necessary industry. But both will need to be fast tracked if we are to succeed in the time we have.